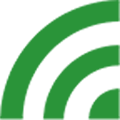
Control del proceso en el circuito de molienda
viernes 11 Ago 2023
Las plantas de procesamiento de minerales han adoptado sistemas avanzados para gestionar eficazmente sus operaciones. Un componente crucial de estos sistemas es la instrumentación, que permite obtener datos en tiempo real sobre diversos procesos. Los datos recopilados se utilizan en bucles de control, lo que permite un control preciso de las operaciones.
La información obtenida de estos instrumentos sirve para el control de procesos, como la regulación de válvulas, bombas y la gestión de la adición de agua de dilución a las pulpas. En esta entrada del blog, exploraremos las principales variables de control que suelen encontrarse en el circuito de molienda.
En primer lugar, analizaremos brevemente cómo gestiona los datos una planta de procesamiento típica a efectos de control de procesos, con la planta María Dama de Colombia como caso ejemplar.
Control de procesos en Maria Dama
María Dama ha adoptado el sistema de control SCADA, un potente sistema de adquisición de datos y supervisión. SCADA desempeña un papel crucial en la recogida de variables y datos de los dispositivos de campo, que luego se transmiten a los servidores y se transforman en valiosa información sobre el proceso.
Esta información en tiempo real se visualiza cómodamente en los monitores de la sala de control del emplazamiento, lo que permite a los operadores responder rápidamente a las necesidades operativas.
Una de las operaciones clave que se supervisan es el circuito de molienda, en el que se pueden seguir fácilmente parámetros cruciales como la producción horaria de mineral procesado. En la fase de separación del mineral, parámetros como la densidad, el caudal, el tamaño de las partículas y la presión suelen estar bajo vigilancia constante para garantizar las medidas de rendimiento.
La información recibida permite a los operarios analizar rápidamente el comportamiento del proceso, lo que agiliza la toma de decisiones y el análisis del comportamiento del proceso para lograr un alto rendimiento y eficiencia de la planta.
Algunas ventajas de los controles avanzados de procesos
(I) Control total de la planta mediante vigilancia
Controlar diversos parámetros, como el tamaño de las partículas y la densidad del lodo, para lograr un proceso de clasificación eficaz en un ciclón tiene muchas ventajas. El ciclón utiliza la fuerza centrífuga para separar las partículas de lodo en función de su tamaño, forma y gravedad específica.
Las partículas más gruesas sedimentan más rápidamente y se desplazan hacia la pared del ciclón, mientras que las partículas más finas se desplazan hacia la zona de baja presión y son empujadas hacia arriba.
Mantener una cierta densidad de los lodos es crucial para una clasificación óptima de las partículas. El ciclón es muy eficaz para la separación de tamaños finos, pero menos eficiente para las partículas de tamaño medio.
Un exceso de agua en el proceso conduce a la producción de más partículas de tamaño medio, que escapan del circuito de molienda a través del rebosadero del ciclón, disminuyendo la eficiencia del molino y permitiendo que tamaños de partículas no deseados entren en las etapas posteriores del proceso.
(II) Clasificación óptima de partículas
Para lograr una clasificación óptima de las partículas, es necesario controlar en tiempo real los cambios en la alimentación del ciclón. El control del porcentaje de sólidos en el flujo de alimentación mediante un densímetro es un aspecto clave para lograr un control óptimo del ciclón. Además, los densímetros también se utilizan para controlar el desbordamiento y el flujo inferior del ciclón, así como la presión y el tamaño de las partículas.
Un contenido excesivo de sólidos puede sobrecargar el circuito de molienda y provocar un rendimiento deficiente de la molienda. Por lo tanto, la densidad de la lechada debe mantenerse dentro de los objetivos especificados y los parámetros establecidos inicialmente por el personal del proceso.
Se puede añadir agua al proceso para diluir la pasta y controlar su densidad, reduciendo así el número de partículas de tamaño medio y evitando una mala molienda causada por la sobrecarga de sólidos.
La medición continua en tiempo real es esencial en el circuito de molienda para garantizar que la densidad se mantiene en condiciones óptimas.
(III) Mejora de la resolución de problemas
La implantación de controles avanzados proporciona una mayor estabilidad al circuito de molienda al gestionar activamente las perturbaciones y mantener las condiciones de funcionamiento deseadas. Esta estabilidad se traduce en un menor tiempo de inactividad, menos interrupciones del proceso y una mayor fiabilidad general.
Cuando el ciclón devuelve mineral al molino de bolas, tanto el volumen total de mineral como la densidad de la pulpa aumentan en el circuito de molienda. Este mineral reciclado se denomina carga circulante. Si el proceso de molienda pierde eficacia, la carga circulante seguirá aumentando hasta superar la capacidad de tratamiento del circuito.
Un densímetro puede aplicarse como sistema de alerta en el circuito de molienda. La medición de la densidad en tiempo real permite detectar el aumento de la carga circulante, lo que permite controlar el proceso antes de que los problemas se vuelvan inmanejables. El tamaño de las partículas es un indicador importante del rendimiento del circuito de molienda y suele medirse con analizadores granulométricos en línea (PSA).
Sin embargo, la falta de disponibilidad de las mediciones de PSA puede perturbar el bucle de control. Para solucionar este problema, se desarrolló un predictor autocorrectivo del tamaño de las partículas en un proyecto de automatización de un circuito de molienda en Sudáfrica.
Este predictor calculaba el valor previsto del tamaño de las partículas basándose en la densidad de alimentación de los purines, el caudal volumétrico y la caída de presión sobre el ciclón. El valor predicho se actualizaba cada cinco minutos. Incluso cuando el valor PSA se perdía temporalmente, el valor predicho se mantenía en estrecha concordancia con el valor real cuando volvía.
En general, las ventajas de los controles avanzados de procesos en el circuito de molienda incluyen una mayor eficacia, una mejora de la calidad del producto, un aumento del rendimiento, una reducción de la variabilidad, la estabilidad operativa, una utilización óptima de los recursos y la supervisión y el diagnóstico en tiempo real.
Estas ventajas contribuyen a la optimización general del proceso y a los beneficios económicos de las operaciones de minería y procesamiento.
¿Recibió nuestra actualización técnica?
Introduzca su nombre y dirección de correo electrónico y le mantendremos informado de nuestras últimas actualizaciones tecnológicas.